La construction d’un bâtiment industriel représente un investissement lourd. Néanmoins, avec une planification rigoureuse et des choix techniques avisés, il est possible de maîtriser le budget sans sacrifier la qualité ni la durabilité. Dans cet article, nous détaillons sept axes d’optimisation à exploiter dès la conception jusqu’à l’exploitation.
1. Soigner la phase de conception
Une conception étudiée en amont permet d’éviter des ajustements coûteux plus tard.
1.1 Standardiser les dimensions
En adoptant des modules (panneaux muraux, dalles de plancher, profilés de charpente) aux dimensions industrielles standard, vous limitez les chutes. Moins de découpes signifie moins de déchets à évacuer et un gain de temps sur la pose.
1.2 Simplifier la structure
Une charpente à portiques préfabriqués ou des poutres en I permettent d’assembler rapidement de grandes travées sans multiples renforts. Cette approche réduit la main‑d’œuvre et nécessite moins de manutention, tout en garantissant une solidité suffisante pour les usages industriels.
1.3 Impliquer tous les acteurs
Dès l’esquisse, réunissez architectes, ingénieurs structure, bureaux d’études et chefs de chantier. Cette démarche collaborative repère les incompatibilités techniques, optimise les sections de ferraillage et anticipe les points singuliers (passage de conduits, plateformes techniques).
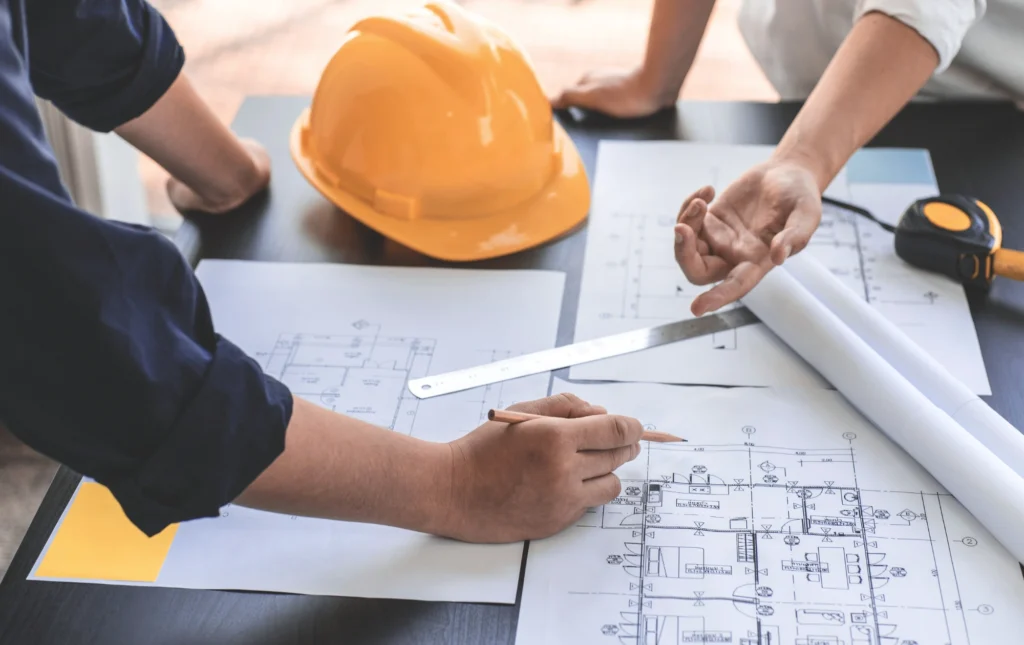
2. Choisir des matériaux et méthodes adaptés
Le choix des matériaux et techniques influe directement sur le coût global et la durée des travaux.
2.1 Privilégier le préfabriqué
Les murs sandwich isolants, les poutres préfabriquées et les escaliers modulaires réduisent considérablement le temps de montage sur site. En usine, la qualité est contrôlée et la pose s’effectue en quelques heures, contre plusieurs jours en traditionnel.
2.2 Favoriser les fournisseurs locaux
Sélectionner des matériaux produits à proximité du chantier (béton prêt à l’emploi, acier ou bois local) diminue les frais de transport et les délais de livraison. Cela renforce également la relation avec les producteurs nationaux et garantit un meilleur suivi qualité.
2.3 Opter pour la durabilité
Un produit plus cher à l’achat (peinture anti-corrosion, isolant haute performance) peut s’avérer plus rentable sur la durée en réduisant les coûts de maintenance et de renouvellement. Pensez cycle de vie : considérez non seulement le coût initial, mais aussi l’entretien et la consommation énergétique engendrée.
Ministère de l’Équipement, Transport et Logistique (Maroc) pour les listes de fournisseurs agréés.
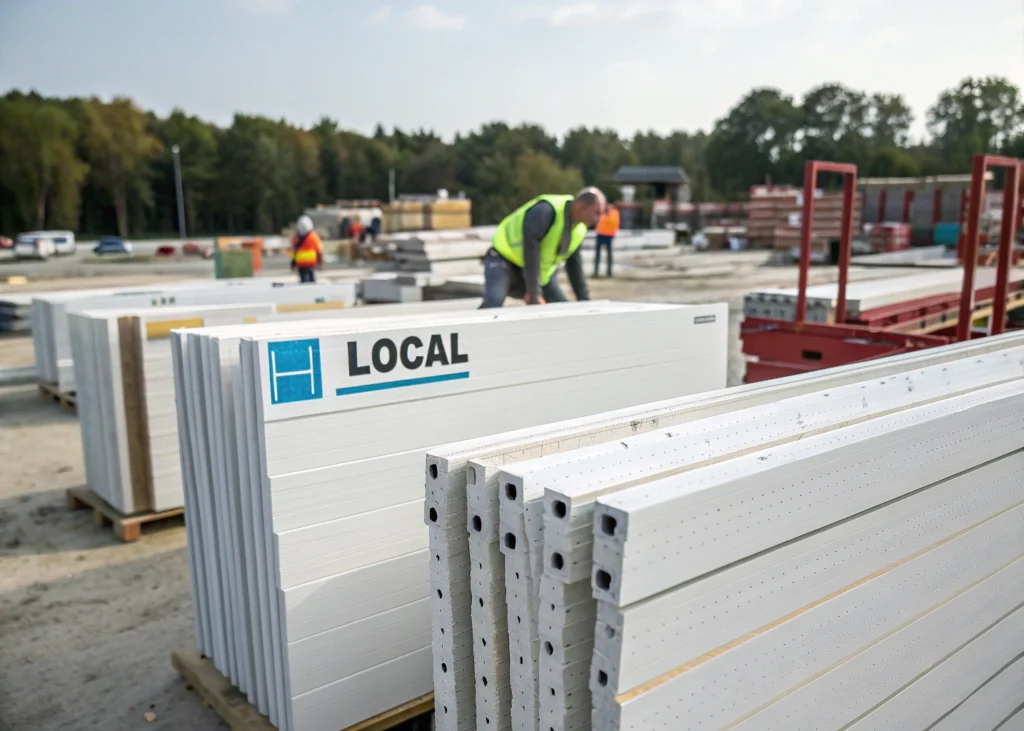
3. Optimiser la logistique de chantier
Une logistique mal pensée génère du gaspillage de temps, de matériaux et d’argent.
3.1 Planifier les livraisons
Établissez un calendrier de livraison calé sur le phasage chantier. Par exemple, les bétons et préfabriqués arrivent juste avant leur pose. Cela évite le stockage long terme, le vol potentiel et les dégradations par intempéries.
3.2 Utiliser des outils de gestion de stock
Un logiciel de suivi permet de visualiser en temps réel les quantités disponibles, les dates de consommation prévues et de déclencher automatiquement les réapprovisionnements. Vous limitez ainsi les ruptures (arrêt de chantier) et les surstocks (frais financiers).
3.3 Structurer les flux sur site
Définissez des zones claires : réception, stockage, préparation, évacuation des déchets. Un plan câblé des voies de circulation réduit les conflits entre engins, accélère les rotations de pelleteuses ou de chariots élévateurs.
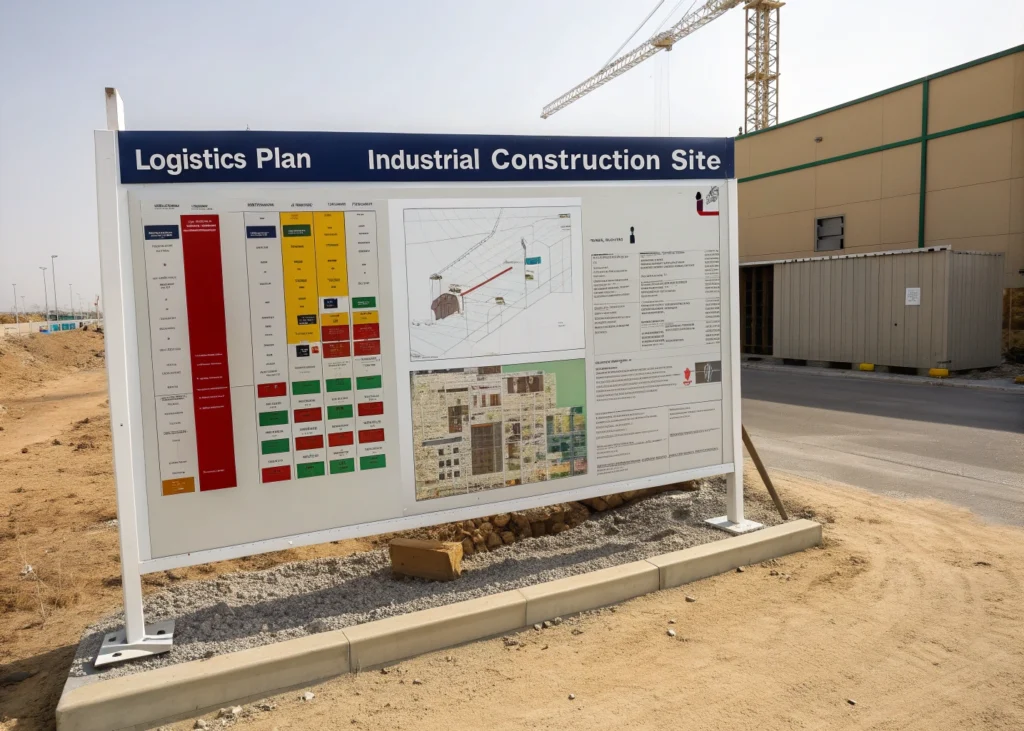
4. Maîtriser la main‑d’œuvre
La main‑d’œuvre est souvent le premier poste de dépense : optimisez-la pour rentabiliser chaque heure de travail.
4.1 Sous‑traitance ciblée
Externalisez les tâches très spécialisées (soudure, dépose de machines, tests non destructifs) auprès d’experts pour éviter la perte de temps et de qualité que peut générer une équipe non formée.
4.2 Formation et process internes
Investissez dans des sessions courtes de formation sur les méthodes Lean ou sur les outils numériques (BIM, tablettes de suivi). Une équipe formée travaille plus vite, avec moins d’erreurs.
4.3 Planning et suivi précis
Établissez un planning par jour et par demi‑journée, avec jalons intermédiaires. Un chef de chantier responsable du respect des étapes réduit le recours aux heures supplémentaires et évite les arrêts coûteux.
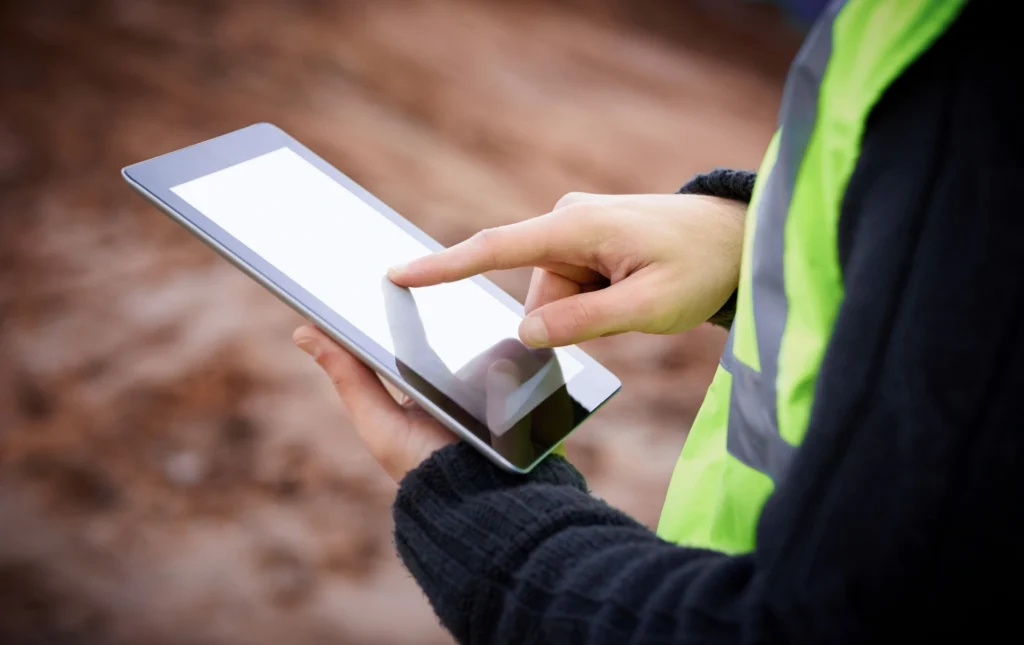
5. Réduire les gaspillages et optimiser la gestion des déchets
Chaque déchet de chantier représente un coût de collecte et de transport.
5.1 Suivi des chutes
Installez des bacs spécifiques pour les chutes de bois, de métal ou de béton. Pesez régulièrement pour identifier les matériaux les plus gaspillés et ajuster les commandes.
5.2 Valorisation sur site
Les gravats concassés sur place peuvent servir de remblai. Les palettes bois réutilisées après réparation limitent l’achat de nouvelles palettes.
5.3 Partenariats avec filières locales
Contractez avec une société de recyclage pour évacuer matériaux triés (béton, ferraille, bois). Un tarif préférentiel peut être négocié pour un volume régulier.
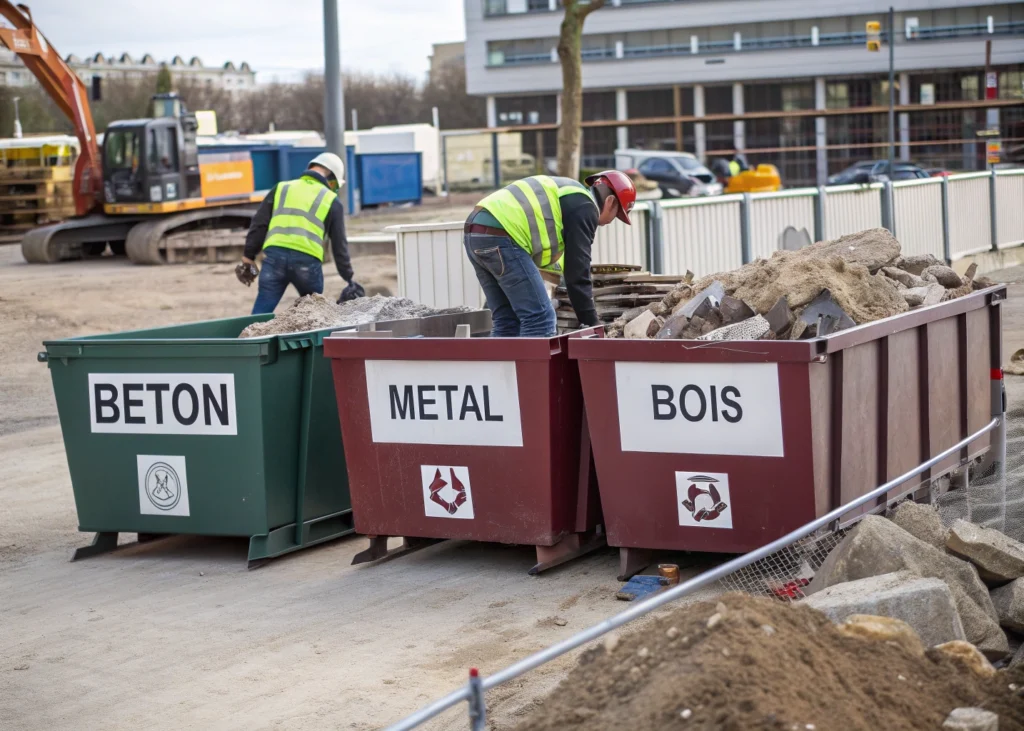
6. Surveiller la performance énergétique
Penser efficacité énergétique dès la construction diminue les coûts d’exploitation.
6.1 Isolation renforcée
Posez des isolants haute performance dans les murs et toitures. Un bâtiment moins énergivore permet de réduire de 20 à 40 % la facture de chauffage et de climatisation.
6.2 Éclairage et automatisation
Installez des éclairages LED couplés à des détecteurs de présence et à une gestion centralisée. Vous limitez la consommation aux seules zones occupées et aux heures d’activité.
6.3 Maintenance préventive
Planifiez des contrôles réguliers (filtrage, graissage, calibrage) sur les systèmes HVAC et électriques. Une panne évitée est un coût évité.
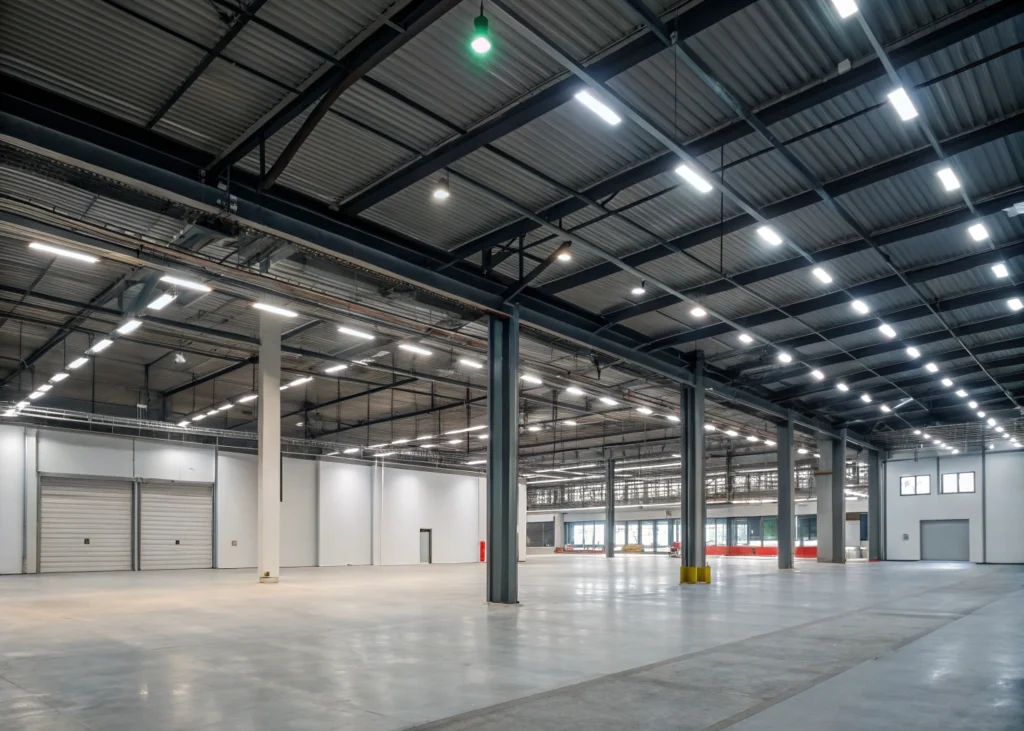
7. Anticiper la fin de vie du bâtiment
Penser à la démolition ou la reconversion dès la conception augmente la valeur résiduelle.
7.1 Choix de matériaux démontables
Optez pour des cloisons, sols technique ou modules d’atelier qui se démontent sans casse. Vous rendez possible une réaffectation ou un démantèlement à moindre coût.
7.2 Flexibilité d’usage
Concevez des zones modulaires, avec réseaux et planchers techniques. Une configuration changeante limite les travaux lourds pour une nouvelle activité.
7.3 Analyse du cycle de vie (ACV)
Réalisez une étude ACV pour comparer les coûts totaux sur 30 ans. Cela guide vos choix vers les composants les plus rentables à long terme.
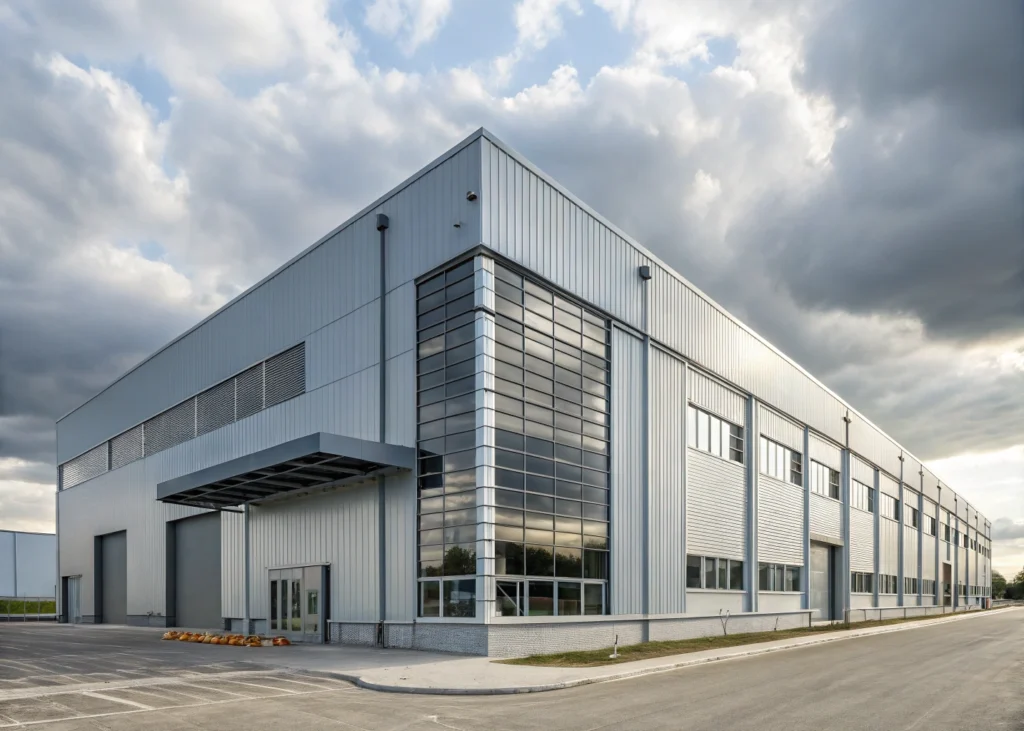
Conclusion
Optimiser les coûts d’un projet de construction de bâtiment industriel exige une démarche structurée. De la conception à la fin de vie, chaque décision technique, logistique ou humaine peut générer des économies substantielles sans compromettre la qualité.
Vous souhaitez maîtriser votre budget tout en bénéficiant d’un accompagnement expert ?
Contactez LAI pour une étude personnalisée et des solutions sur mesure qui allient performance, durabilité et maîtrise des coûts.